Tag: tailings storage facility
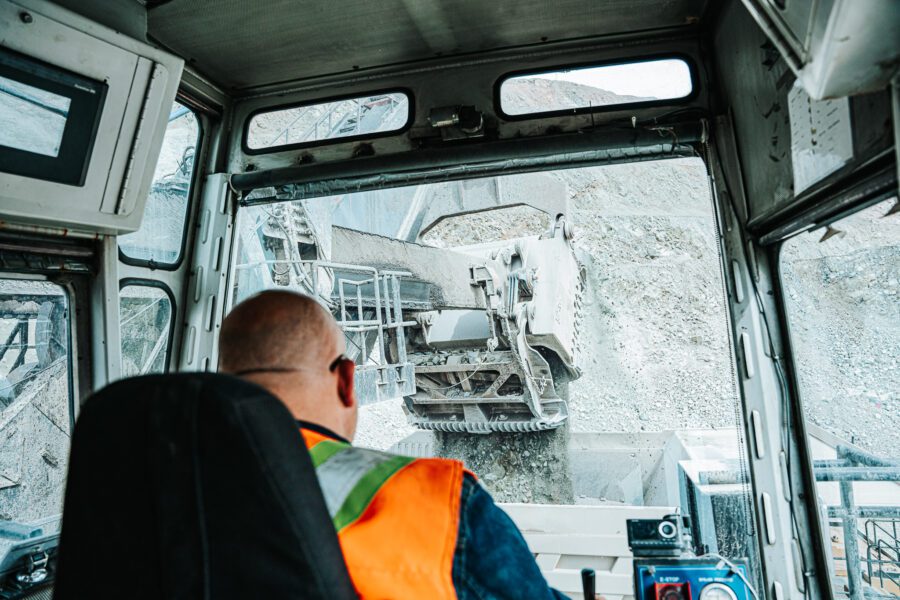
Why We’re Raising the Height of Our Tailings Storage Facility
April 15, 2025
As part of regular mine operations at Mount Polley, we recently received government approval to raise the height of our tailings storage facility (TSF) by 4 metres. This kind of work is a normal and necessary part of operating any mine that s… Read more »
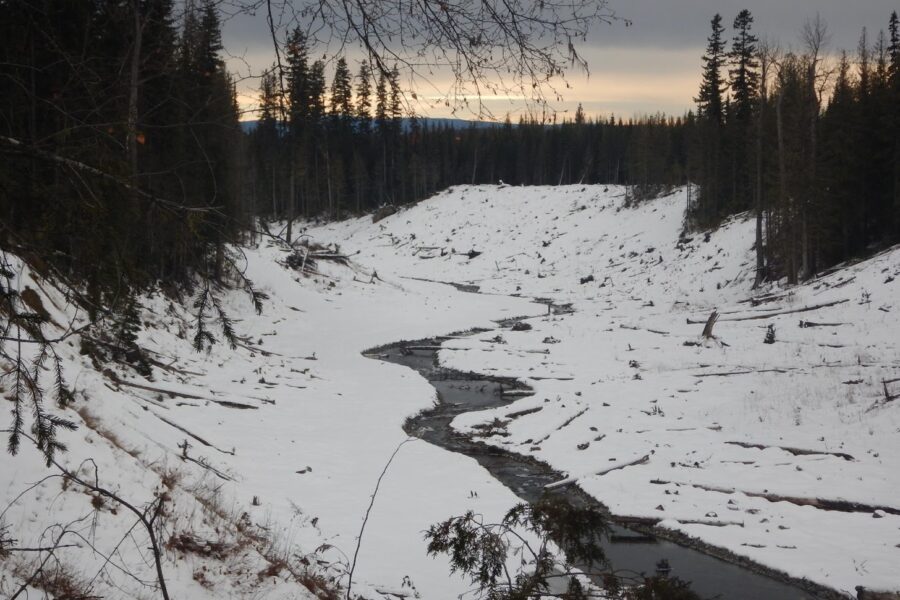
A letter from the Mount Polley Team
March 3, 2021
Happy Holidays – we hope that everyone enjoyed a joyous holiday season and wish you all the best for 2021.
A Covid-19 update – Mount Polley employees continue to take additional precautions to minimize the risks of COVID19 tra… Read more »

Briefing Note on Hamilton et al 2020 paper
September 9, 2020
The following provides some comments from Mount Polley Mining Corporation (MPMC) on the Hamilton paper (Hamilton, et al. 2020)[1] regarding Quesnel Lake in relation to the TSF Breach at Mount Polley. The note is divided into general comm… Read more »

Mining and Mineral Processing at the Mount Polley mine
July 10, 2020
In the Mount Polley
Mine, run-of-mine ore from the open pits and underground is hauled to the
crusher. The crusher has three stages of
crushing involving five crushers, twenty conveyors and four sets of screens. Ore is dumped… Read more »
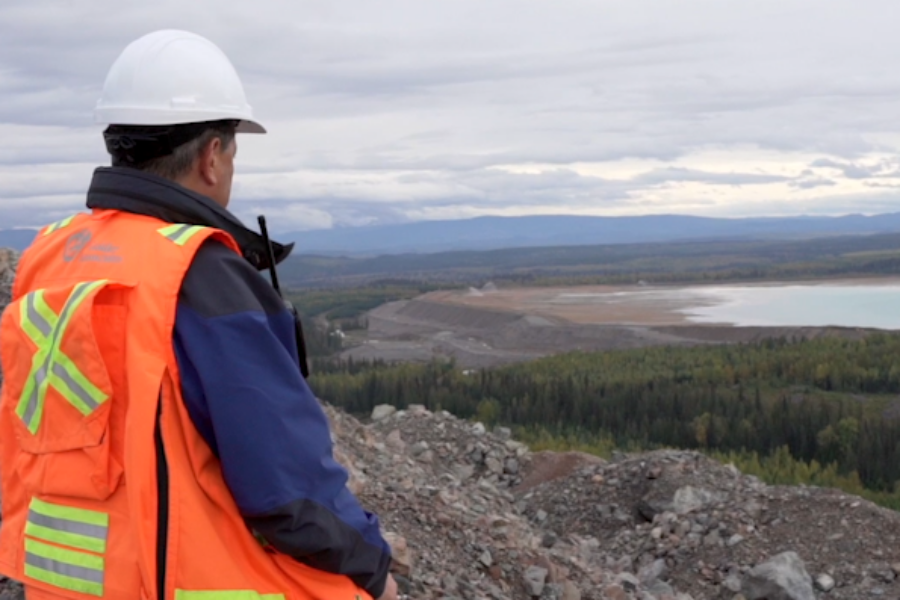
Tailings – What are they and what is in the Mount Polley tailings?
March 10, 2020
First, what are
tailings?
Tailings are essentially crushed rock,
and are the leftover material after the minerals containing the “elements of
interest” have been removed. At Mount Polley the elements of interest are
copper, gold and sil… Read more »